Tres ejemplos de innovación 18/10/2013 |
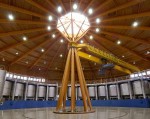
Tres Ideas desarrolladas por varias empresas para mejorar sus capacidades
Del problema a la oportunidad
Tecnalia desarrolla una tecnología para el tratamiento de polvos de acería
Cómo convertir un problema en oportunidad está en la esencia de Digimet, una de las últimas empresas gestadas en el seno de Tecnalia, que aspira, gracias a una tecnología que trata el polvo de acería, a convertirse en un referente mundial en el tratamiento de estos residuos.
El desarrollo de un nuevo horno metalúrgico, en el que desde 2008 llevan trabajando ocho investigadores y tres empresas que han colaborado con la ingeniería y el suministro de equipos, permite extraer hierro y zinc de alta calidad a partir de los polvos de acería.
Tecnalia explica que la patente posibilita dar solución a un problema medioambiental, la gestión de los residuos de las acerías, para convertirlo en una oportunidad de negocio, tanto para las propias compañías del sector como para las especializadas en el tratamiento de estos desechos o para los fabricantes de zinc y de equipos.
Un horno de acería
La tecnología “permite una oportunidad para las propias acerías para valorizar sus residuos, al mismo tiempo que ahorran en costes para deshacerse de ellos. En el caso de los tratamentistas, este horno supone una herramienta más eficiente de las que ahora disponen”, enumeran fuentes de Tecnalia en referencia a un mercado, el de la gestión de estos desechos, que mueve unos 1.000 millones de euros al año en todo el mundo.
La idea del proyecto surgió para intentar dar respuesta al problema planteado por la entrada en vigor en 2007 de una normativa europea que prohibía la deposición en vertederos de los polvos de acería, explican las mismas fuentes. Además, el nuevo horno no solo supone la recuperación de zinc y hierro, sino también la reducción del consumo energético y, por tanto, de las emisiones de gases contaminantes a la atmósfera.
Los procesos para el tratamiento del polvo de acería que existen en el mercado generan 700 kilos de escoria metalizada por cada tonelada de residuo tratado. Con el nuevo horno desarrollado por Tecnalia esa cifra cae hasta los 300 kilos, lo que se podría considerar “residuo cero, ya que la escoria final exenta de metal es apropiada para su uso en una cementera”, precisan desde el centro de investigación.
Digimet, creada por Tecnalia y el fondo de inversión privado Kereon Partners, se suma así a las numerosas empresas de base tecnológica desarrolladas por la corporación vasca, de las que 25 se mantienen vivas y de las cuales todavía participa en 17.
Hidrógeno allá donde haga falta
Alhymotion crea una patente para la obtención del gas a través de aluminio
Seis emprendedores están detrás de Alhymotion, una empresa de base tecnológica que ha desarrollado una patente para la obtención de hidrógeno en cualquier lugar y a demanda. Como explica su responsable, Roberto Fernández, el equipo, movido por la máxima de contribuir a la creación de “un nuevo modelo energético más amable con el medio ambiente”, lleva dos años trabajando para conseguir transformar aluminio en hidrógeno para la creación de distintas aplicaciones con el apoyo de un consorcio del País Vasco.
La tecnología que han desarrollado permite la obtención del gas a través de la actuación sobre residuos de aluminio, de tal forma que se solucionan dos de los problemas ligados al tratamiento y manejo del gas: el transporte y el almacenamiento. “Es un gas con un gran poder energético por unidad de masa, pero al ser tan ligero, necesita de métodos caros y complejos para su logística, métodos que además pueden suponer un riesgo por el manejo de gases inflamables a altas presiones”, explica Fernández. Estos dos problemas fueron los que empujaron a los miembros de Alhymotion a buscar “otras tecnologías o para disponer de sistemas de generación”.
Estudio para estación de repostaje con el sistema Alhymotion en Düsseldorf
La patente desarrollada por los seis emprendedores utiliza los metales como “combustible para producir el hidrógeno on site y on demand de gran pureza y caudal necesario para todas las aplicaciones posibles o para ser directamente una fuente de suministro de energía”, detalla el responsable de la compañía.
La tecnología, un ejemplo de la “economía del hidrógeno”, es decir, como alternativa a los combustibles fósiles, no produce emisiones contaminantes y tiene múltiples aplicaciones.
El equipo de Fernández trabaja actualmente en el desarrollo de la aplicación Alhyself, orientada a industrias que producen diversos residuos de aluminio, lo que les permitirá tratar los restos del metal consiguiendo energía, a la vez que se reduce el impacto medioambiental. Para ello, Alhymotion ha constituido un consorcio con Ingeinnova, Bostlan, Reflectia y Zigor, y con las asociaciones FEAF de fundidores y AFM de máquina-herramienta.
La patente desarrollada permite además otros usos o aplicaciones, como, por ejemplo, la alimentación de sistemas basados en la tecnología Fuel Cell, es decir, sistemas de respaldo ante fallos de suministro de energía o generación de hidrógeno para repostaje de vehículos.
El vino estudiado con mayor detalle
Viña Real dispone de la última tecnología para el análisis de las uvas
Sistemas para la recogida de la uva por gravedad y estudios de la UPV para analizar algunos de los componentes del fruto convierten a la bodega Viña Real, sita en Laguardia y propiedad de CVNE, en una de las instalaciones del sector más punteras, según explica María Larrea, directora técnica de la compañía.
Las instalaciones alavesas de la firma, que cuenta además en La Rioja con una bodega con 134 años de historia, suponen una mezcla de conocimiento centenario y técnicas del siglo XXI. La innovación tecnológica acompaña a todo el proceso de elaboración del vino.
Viña Real emplea sistemas de “vinificación no agresiva”, dice Larrea. “Se trata de un método de transporte del mosto que combina un sistema de depósitos volantes, familiarmente conocidos como ovis, objetos volantes identificados, grúas y decantación por gravedad, sin necesidad alguna de bombas de impulsión ni de tuberías”, añade. Esta técnica hace que el fruto sufra lo menos posible desde su recolección hasta su llegada a la bodega.
Nave de vinificación de la bodega Viña Real en Laguardia
La tecnología y la innovación continúan una vez dentro de la barrica. La bodega realiza, en colaboración con la UPV, estudios constantes de los polifenoles y taninos, dos sustancias presentes en la uva y encargadas, entre otras cosas, de determinar el color del vino. “Se sigue toda la evolución, desde la recepción de la uva, su comportamiento dentro de la barrica, hasta su salida en botella”, ilustra Larrea, lo que supone una vigilancia constante en cada fase del proceso.
Los estudios que realiza la UPV, que analizan los componentes del hollejo y de las pepitas de las uvas, permiten a la bodega determinar, entre otras cuestiones, qué lotes de uva son los indicados para cada tipo de barrica, el tiempo, el sabor o la temperatura de fermentación.
CVNE ha comenzado además a desarrollar una experiencia piloto que consiste en una alta densidad de plantación de vides por metro cuadrado, muy superior a la tradicional. De las 3.000 plantas por hectárea se pasa hasta las 7.000, lo que supone que cada vid, al tener que hacer un mayor esfuerzo por sobrevivir, da menos frutos, pero con una mayor calidad, según arrojan los resultados del proyecto, realizado en colaboración con la Universidad de La Rioja.
Fuente: El País-Pais Vasco